Generator connecting rods reuse or replacement
- BY BISON
Table of Contents
The power which is generated by the piston in the combustion chamber of a generator engine is transferred to the crankshaft through the connecting rod. While transmitting such a tremendous amount of power, the connecting rod is subjected to different stresses, making it vulnerable to damage. Therefore, the connecting rod bolt is used to connect the connecting rod and the connecting rod bearing cap under the considerable stress generated when the generator engine is running.
The most common type of generator connecting rods used in generators is the oblique or crosscut connecting rods, which consist of two parts.
Generator connecting rods reuse or replacement? Although it can be reused, always check for wear. If damaged, choose a replacement to ensure optimal performance.
What factors need to be considered?
The following points must be considered when checking whether diesel engine connecting rods are reused or replaced:
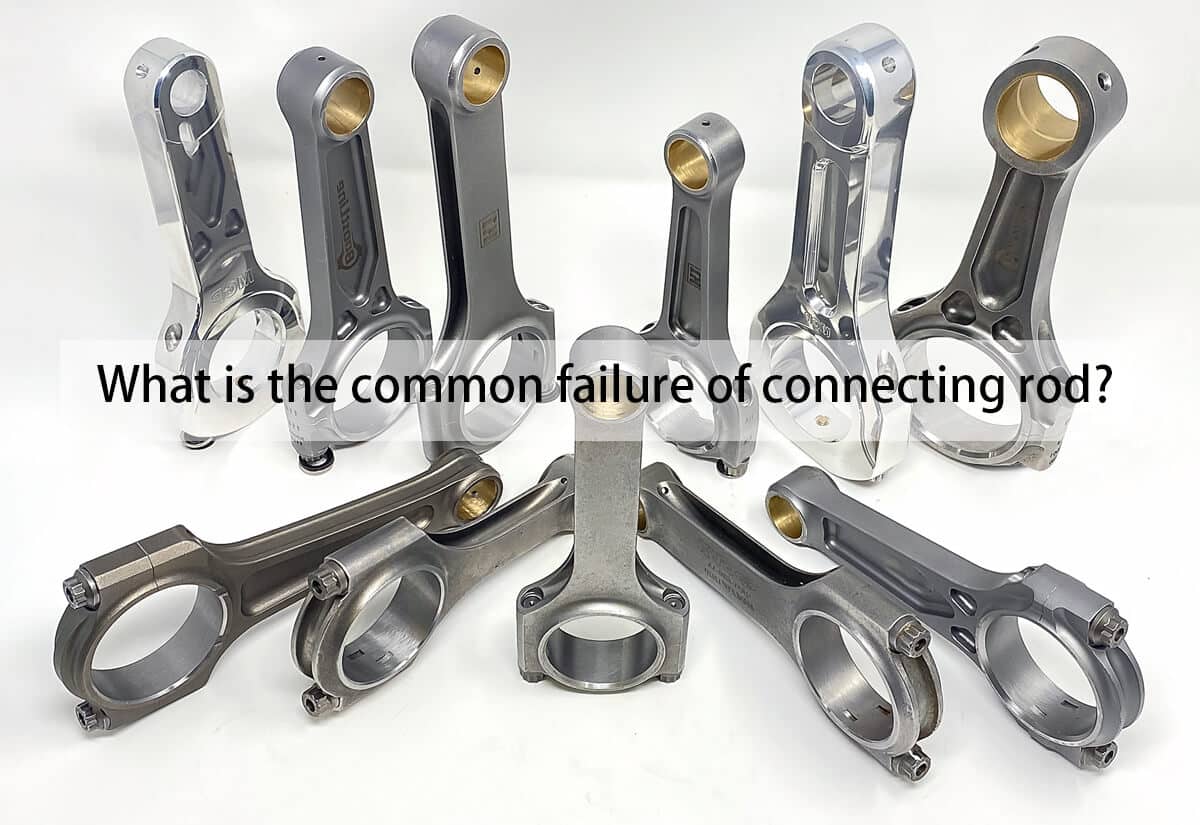
1) Checking the ovality of the connecting rod
First, check the ovality of the connecting rod by tightening both parts with the rated torque. The bore micrometer is used to determine the correct and current ovality of the connecting rod. If the ovality is exceeded, the connecting rod must not be reused.
2) Check the connecting rod for wear and corrosion
Check the connecting rods for wear and corrosion. If wear is minimal, it can be removed with an oil stone. Never use a sander or scraper. Worn connecting rods must be replaced.
3) If using connecting rods with fretting wear, check for cracks
Only slight fretting wear can be allowed on the connection for reuse if there are no cracks on the surface. If the fretting is minor and treated with a whetstone, the entire area must be rechecked with a magnaflux, which can detect tiny, invisible cracks to the naked eye.
4) Check the cracks between the connecting rod and the bearing cover
Use the die flaw detection test to check whether there are cracks in the serrations and holes between the connecting rod and the bearing cover. Rods should only be used if no damages are detected. If there is a small crack at the serration of the connecting rod bearing cap, replace it with a new spare part.
5) Replace the connecting rod and the connecting rod bearing cap together
Replace the connecting rod and the connecting rod bearing cap as a whole. Do not replace individual parts of the connecting rod to avoid damage, as the serrations are machined in pairs to position the two halves relative to each other.
6) Serrations should not be reworked
Serrations on connecting rods/bearing caps or bores should not be reworked, even with minor damage or indentations.
7) Bearing a shell with fretting on the back should not be used
The bearing shell with fretting on the back cannot be used with the connecting rod and should be replaced.
8) Make sure that the bolts and bearings are of the same type when replacing
If the connecting rod is replaced, the same type, same connecting rod bolts, and bearings should be used. Review older generator data to confirm which bearing size (undersize or oversize) to install when updating the casing.
9) Replace connecting rod bolts as a set
Connecting rod bolts are used and replaced as a set. If the connecting rod is replaced with a spare, the connecting rod bolts from the old connecting rod must not be used with the new spare.
10) Correct sequence and tightening torque
Once the decision is made to reuse or replace the connecting rods, the engineer’s office must ensure that he knows the correct assembly sequence (front/rear side, connecting rod pair and bearing cap, etc.) Tightening procedure, apply the rated tightening torque to the connecting rod bolts.
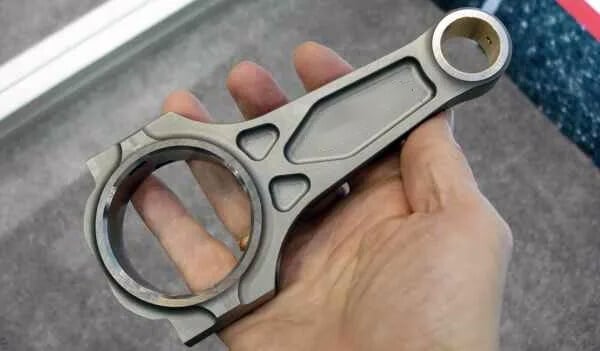
When Can a Generator Connecting Rod Be Reused?
Reusing a generator connecting rod is an option in certain scenarios, usually under specific conditions. Here’s when you can consider reusing it:
Visual inspection: Start with a visual inspection of the connecting rod. Look for any obvious signs of damage, such as cracks, scoring, or discoloration. If you see any of these, it’s probably best to replace the connecting rod.
Check for straightness: A connecting rod must be perfectly straight to function properly. You can check this by rolling the rod on a flat surface. If it wobbles or doesn’t roll smoothly, it may be bent and should be replaced.
Measure for size: Over time, the big-end bore of the connecting rod can become elongated or “out-of-round,” which can lead to engine damage. Use a micrometer to measure the bore diameter. If it’s not within the manufacturer’s specified range, you’ll need to replace the rod.
Successful magnaflux testing: Magnaflux testing is a non-destructive testing method used to detect minute cracks and flaws in ferrous materials. If the connecting rod passes this test, it may be reusable.
Expert inspection approval: Lastly, and most importantly, an expert inspection should confirm that the connecting rod is fit for reuse. Professionals can assess the structural integrity of the rod and give an accurate judgment.
Check for straightness: A connecting rod must be perfectly straight to function properly. You can check this by rolling the rod on a flat surface. If it wobbles or doesn’t roll smoothly, it may be bent and should be replaced.
Measure for size: Over time, the big-end bore of the gnerator connecting rod can become elongated or “out-of-round,” which can lead to engine damage. Use a micrometer to measure the bore diameter. If it’s not within the manufacturer’s specified range, you’ll need to replace the rod.
Inspect the bearing surface: The bearing surfaces on the connecting rod should be smooth and free of any pitting or scoring. If there’s any damage to these surfaces, it could lead to bearing failure, so it’s best to replace the rod.
Check the bolts: Finally, check the connecting rod bolts. These can stretch over time and lose their clamping force. If they’re not within the manufacturer’s specified range, they’ll need to be replaced. And since you usually have to replace the entire rod when you replace the bolts, this could mean it’s time for a new connecting rod.
Remember, in the case of diesel generators, an ounce of prevention is worth a pound of cure. Regular inspections and maintenance can extend the life of your equipment and save you money in the long run. So whether you decide to reuse connecting rods or replace them, make sure they are in good working order to keep your generator running smoothly.
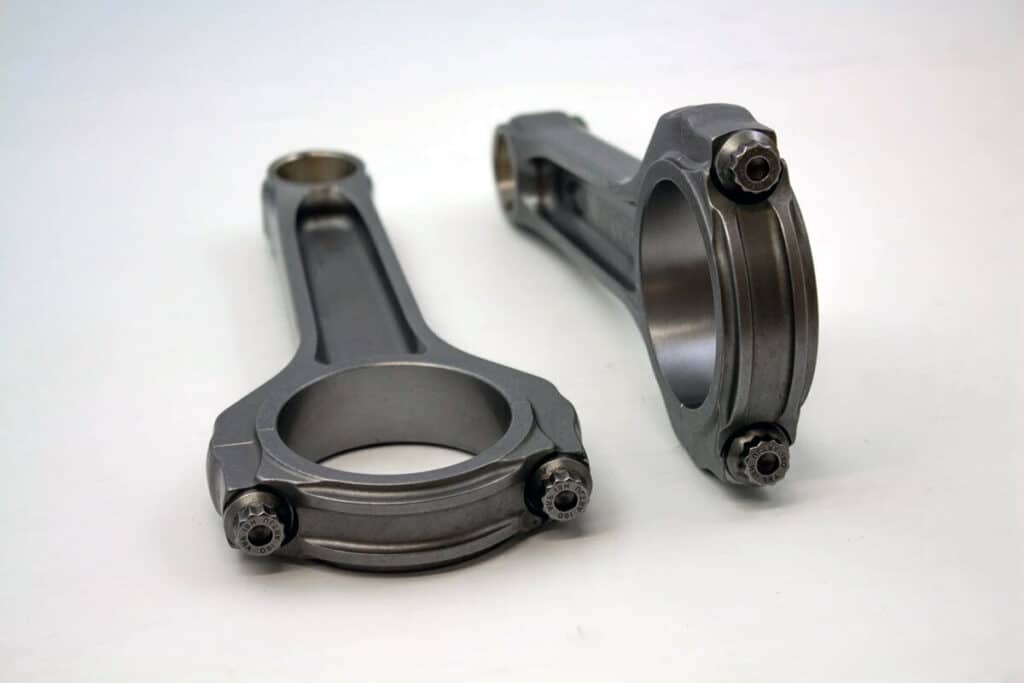
When should you replace your generator?
When it comes to maintaining the diesel generator, one of the key components that often comes into question is the connecting rod. This critical engine piece connects the piston to the crankshaft, transferring motion and power. The longevity of a generator is significantly influenced by the health of the connecting rod, so it’s vital to know when it should be replaced.
When the Connecting Rod is Damaged Beyond Repair
If your connecting rod is damaged beyond repair, replacement is the only viable option. Damage can occur due to various reasons such as mechanical failure, overheating, or oil starvation. Signs of a severely damaged connecting rod might include bending, breaking, or even holes burned through the rod. In such cases, the connecting rod has lost its structural integrity, and continuing to use it may lead to catastrophic engine failure.
When the Connecting Rod is Worn Beyond Specification
Wear and tear is inevitable with any engine component, and connecting rods are no exception. Over time, due to friction, heat and pressure, connecting rods can wear beyond the tolerances specified by the connecting rod manufacturer. This wear can lead to decreased performance, increased fuel consumption, and potential engine damage. If wear exceeds the specified limits, it is recommended that the connecting rods be replaced to maintain optimum performance and prevent further engine damage.
When the Connecting Rod is Being Reused with New Bearings and Bolts
It is a common practice to reuse connecting rods during engine overhauls. However, it is critical to ensure that the connecting rods still meet the parts manufacturer specifications and are not structurally compromised. A thorough inspection by a BISON technician is highly recommended if this method is being considered.
How to remove and install generator connecting rods?
Disassemble the engine: Disconnect power, remove external components, and open the cylinder head to access the pistons and connecting rods.
Remove the old connecting rod: Detach the connecting rod from the crankshaft and piston by removing the securing bolts. Check for wear or damage.
Install the new connecting rod: Attach the new rod to the piston, then to the crankshaft. Ensure correct lubrication and bolt torque as per manufacturer guidelines.
Reassemble the engine: Replace the cylinder head and external components. Reconnect power, perform a visual check and run the generator to ensure proper installation.
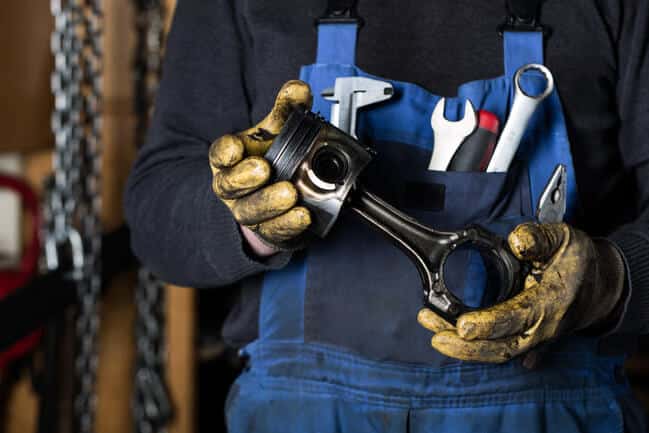
Conclusion
Evaluating the reuse or replacement of generator connecting rods is a critical decision for many people to make. A slight mistake in making the right choice can lead to severe damage to the generator, sometimes even cause and effect.
These are some of the necessary basic checks that China BISON suggests you should perform to maintain the longevity and efficient performance of your generator.
FAQ
how long do generator connecting rods typically last?
Tensile failure from high engine speeds, the impact force of the piston hitting a valve because of a valvetrain issue, rod bearing failure typically resulting from a lubrication problem, or improper installation of the connecting rod are all typical reasons for connecting rod failure.
can the connecting rod be replaced?
The connecting rod can only be replaced by removing the piston from the engine. The pistons can only be removed from the top, which means the cylinder head has to be removed from the engine.
contact us
Please complete our contact form and we will soon get back to you with expert advice.
business
Get in touch to speak with our experts!