Internal vibration of diesel generator set
- BY BISON
Table of Contents
The diesel generator‘s structure includes electrical and mechanical parts, which is also an electromechanical combination. Therefore, its failure is divided into two kinds of analysis. The cause of diesel generator vibration failure is also divided into two parts. Generally, diesel generator vibrations are caused by unbalanced rotating parts or electromagnetic or mechanical faults.
The unbalance of the rotating part is mainly caused by the unbalance of the rotor, coupling, and transmission wheel. The solution is to find the rotor balance first. If there are large drive wheels, brake wheels, or couplings, separate the balance from the rotor. Find a good balance point if there are large transmission wheels, brake wheels, couplings, and split rotors. Then there is the mechanical loosening of the rotating part. If the iron core bracket is loose, the oblique key and the pin shaft are loose, the rotor is not fastened, etc., it will cause an unbalance of the rotating part.
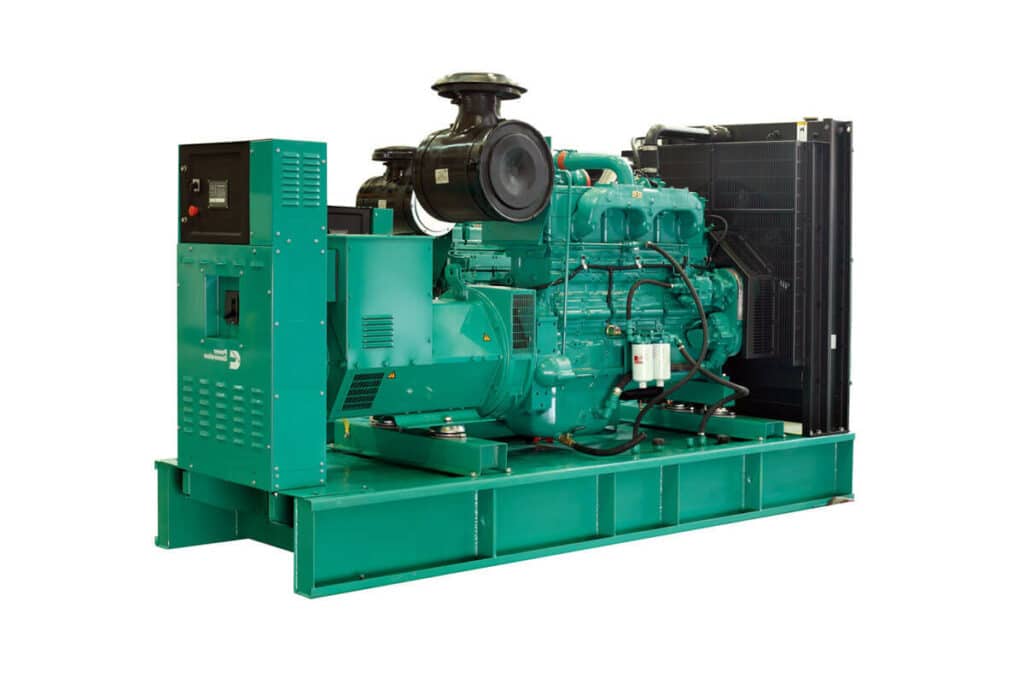
The main problems of the mechanical part are as follows:
- The linkage part of the shaft system is misplaced, the center lines do not coincide, and the alignment needs to be corrected. The cause of this failure is mainly caused by poor alignment and improper installation during the installation process. Another situation is that the centerlines of some interlocking parts coincide in the cold state. Still, after a period of operation, the centerline breaks due to the deformation of the rotor fulcrum and the foundation, resulting in vibration.
- The gears and couplings related to the generator are faulty. This kind of failure is mainly manifested as poor gear meshing, severe tooth surface wear, poor wheel lubrication, skewed coupling, misalignment, toothed coupling tooth profile, incorrect tooth pitch, excessive clearance or extreme wear, which will cause unavoidable damage.
- The load driven by the generator conducts vibration. For example, the steam turbine of the steam turbine generator vibrates, and then the motor drives the fan, and the water pump’s vibration causes the motor’s vibration.
- Structural defects and installation problems of the generator itself. This kind of failure is mainly manifested in the ellipse of the journal, the bending of the shaft, the gap between the shaft and the bearing bush is too small or too large, and the rigid foundation of the bearing housing, the base plate, the parts and even the entire generator installation foundation are insufficient. The generator and the base plate need to be improved. The fixing needs to be firm; the anchor bolts are loose, and the bearing seat and the bottom plate are loose. If the gap between the bearing and the shaft pad is too large or too small, it will not only cause vibration but also cause abnormal lubrication and abnormal temperature of the bearing pad.
Electromagnetic issues cause the failure of the electrical part
- It mainly includes the short circuit of the rotor winding of the asynchronous wound motor, the wrong connection of the stator of the AC motor, the short circuit between the turns of the excitation winding of the synchronous motor, the misalignment of the excitation coil of the synchronous motor, the broken bar of the rotor of the asynchronous cage motor, and the variable stator and rotor air gap cause the deformation of the rotor core, resulting in unbalanced air gap flux, causing abnormal vibration.
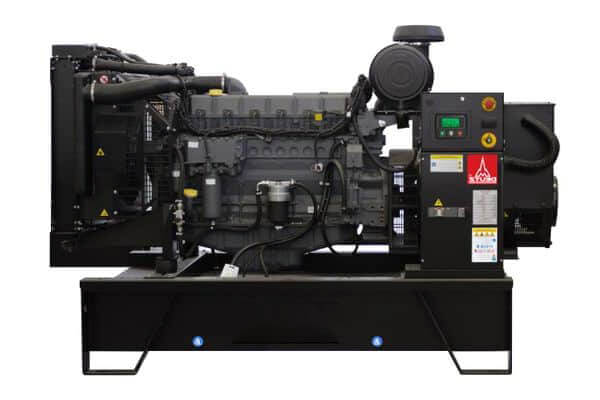
Diesel generator set internal vibration isolation
Gensets are protected from self-excited vibrations without isolation. Some generator sets are designed to absorb all normal vibrations generated internally and most external shock loads.
Not so in the generator environment. Idle generators, auxiliary equipment such as switches and relays, and building structures can be adversely affected by vibrations from an operating diesel generator.
Vibration types
There are two generator set vibration types: torsional and linear.
Torsional vibrations are caused by combustion forces exerted on the engine crankshaft, transmitted throughout the rotating mass. Except for particular installations, the correct matching of the engine and generator set at the factory completely avoids this vibration.
Linear vibrations can have many causes, usually related to shaking and noisy machinery. Its exact nature is often brutal to define without instrumentation since the total vibration measured is approximately the sum of the vibration sources.
Engines vibrate due to combustion forces, torque response, a combination of structural mass and stiffness, and manufacturing tolerances of rotating components. These forces can create various undesirable conditions, from unwanted noise to high-stress levels and eventual failure of engine or generator components. At engine speeds where resonance occurs, vibrational stresses reach damaging levels. Resonance occurs when the system’s natural frequency coincides with the engine excitation. The entire engine-generator system must be analyzed for critical linear and torsional vibrations.
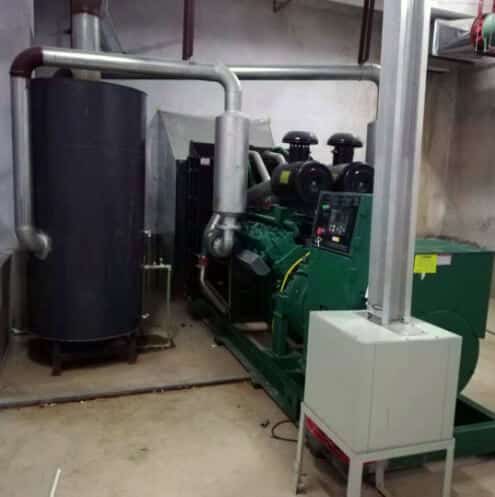
Vibration effects
Rotating machinery such as a running diesel generator set will always experience some vibration, so it is best to isolate the equipment. The device should not be placed directly on rocks, soil, steel or concrete. These materials can transmit vibrations over long distances.
The resonance of specific generator set frequencies with the natural frequencies of building structural components can cause damage to certain types of buildings.
The measured vibration is approximately the sum of all vibration sources. Testing can determine the source.
Generators can be isolated from the surrounding environment using bulk isolators such as inertia blocks or commercial isolators.
Bulk isolators are the more expensive and complex of the two systems. It consists of a big block on which the generator set is mounted. The block is surrounded by fiberglass or cork, insulating it from the surrounding structure.
Rubber pads sometimes dampen the high frequencies that cause noise, but the most common device is a spring-loaded isolator. It provides approximately 95% isolation of all vibrations and eliminates the need for inertial masses.
Spring isolators are placed under the generator rails but aren’t bolted to the floor unless the unit is paralleled with other generators or located in an earthquake-prone area. Spring isolators are most effective when directly under the engine and generator mounting feet.
Care must be taken to ensure that the springs can bear the weight of the generator set. If the spring is fully compressed, all vibrations are transmitted directly to the structure it sits on.
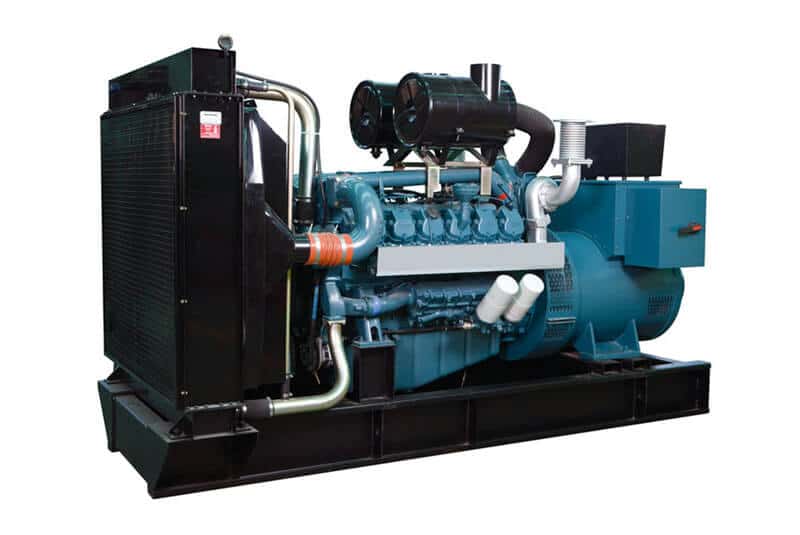
Consider idle units
Units not operating may be damaged by vibrations from nearby operating units. Since the idler has no oil pressure to keep the internal components lubricated, the vibrations can cause severe damage. Here, spring isolators minimize the effects of vibrations.
Fuel lines, exhaust lines, and electrical connections all transmit vibrations. It’s a waste of effort to provide installation protection if those connections are specified to have vibration-limited connections. Each connection must be isolated flexibly to provide maximum vibration dampening.
Resonance in piping systems can also be reduced by suspending supports at unequal distances. To attenuate low-frequency vibrations, specify spring-loaded isolator pipe hangers. Use rubber or cork-lined hangers to minimize high-frequency vibrations.
Specify that hangers are installed at uneven intervals to minimize piping vibration problems.
The complete system can be tested to ensure that the vibrations are not excessive. If the structure (Genset Basic Structure: A Comprehensive Guide) is sensitive to vibrations from generator set operation, such tests should be considered before commissioning the equipment.
Vibration issues can cause considerable damage and are best addressed when the spec is written. Adding spring isolators or inertia blocks and flexible connections on pipes and wires can prevent difficulties later.
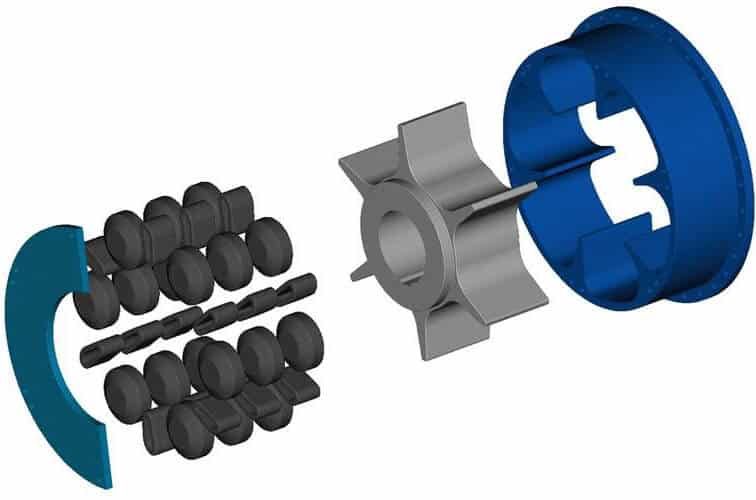
Couplings eliminate internal vibration in diesel generators
BISON rubber compression couplings are the perfect solution for protecting gas, and diesel-driven generator sets from the catastrophic effects of torsional vibration and resonance, which can occur if aligned with the system’s natural frequency.
Torsional vibration is an inherent characteristic of any internal combustion engine due to the pulsation, or torque peak, experienced by the piston during the power stroke when the fuel and air mixture is ignited. Every pulse or torque peak causes an imperceptible twist of the drive shaft, and when a lot of power is involved, the forces involved can be overwhelming.
All physical systems have an inherent frequency of vibration — sort of like a bell. Suppose an external force is applied to a method that coincides with its natural frequency; amplification occurs, known as resonance. Such resonances can be very destructive, as shown in the most famous case of the Tacoma Narrows Bridge collapse in the United States in 1940 when the wind gust frequency coincided with the bridge’s natural frequency.
Likewise, suppose the torsional vibrations coincide with the system’s natural frequency on a diesel or gas engine-driven generator set. In that case, the results can be disastrous or at least shorten component life and significantly increase maintenance and operating costs.
Rubber compression couplings eliminate these problems because the rubber mass inside the coupling is carefully selected to dampen vibrations and keep the natural frequency away from the engine’s operating speed. Couplings provide drive through a compressed rubber mass, hence the name compressed rubber.
This type of flexible coupling is maintenance-free, inherently fail-safe, and a better choice than rubber shear-type flexible couplings prone to early fatigue failure on diesel and gas drive systems. BISON rubber compression couplings can operate in temperatures up to 200°C and offer misalignment capability and blind suitable options if required.
Conclusion
So we discussed reducing the internal vibration of the diesel generator set. We hope you now understand why there are vibrations and what are different methods to reduce them.
If you still have any questions, feel free to contact us. We are the OEM and wholesale supplier of generators of all types.
Diesel Generator Set Internal vibration FAQ
What is the vibration limit of a diesel generator?
Correspondingly, the permissible vibration level of a diesel engine vibration is 45mm/s, and that of the generator is 20 and 28mm/s. If the vibration level of the generator is below 20 mm/s, it will not be damaged.
How to measure vibration in a generator?
Standard tests for generator vibration testing include:
- Bump testing of stator end windings and phase connectors.
- Global modes of end winding baskets.
- Core modes of stators.
How do I stop my generator from vibrating?
Another great way to reduce noise is to limit it at the source. Placing anti-vibration mounts under the generator isolates vibrations and reduces noise transmission. There are many different options — rubber mounts, spring mounts, and dampers — and your choice will depend on the decibel level you need to achieve.
contact us
Please complete our contact form and we will soon get back to you with expert advice.
business
Get in touch to speak with our experts!
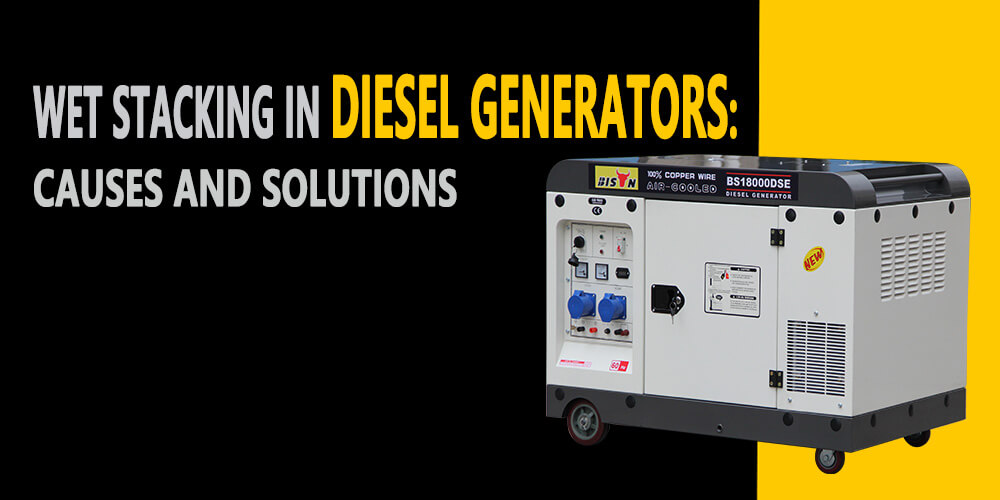
wet stacking in diesel generators: causes and solutions
BISON explores the causes and effects of wet stacking, its impact on diesel generator performance, and offers practical solutions to lessen these effects.

How to charge battery with generator?
This guide is tailor-made for you. In it, BISON delve into the basics of battery charging and explore how to effectively charge your battery with a generator.

How far away should the generator be from the home?
Want to know how far you should place the generator from your home for safe operation? Then read this in-depth guide. Let’s get started.

Diesel generator running in rainy weather
Want to know whether you can run a generator in rainy weather or not? Or how to use a generator in rainy weather? Then this blog post is for you. Let’s get started!

How many dB is a quiet generator?
Want to know how many dB is a quiet generator? Read this blog post, you’ll only know the answer to this question but also more information on quiet generators.

how to check and add coolant to a generator?
We will provide you with a step-by-step guide on how to check and add generator coolant to ensure that your generator stays in tip-top shape.